Gas turbine
Gas turbine generation produces very low toxic emissions of CO and HC and operates on a variety of fuels, including natural gas. The waste heat is dissipated almost entirely in the exhaust, which can then be used for boiling water in a combined cycle or for co-generation. EETS has experience in designing gas turbine generation systems that utilize natural gas.
SPOTLIGHT
Gas turbine Projects
McClellan AFB, California
SMUD – McClellan Gas Turbine
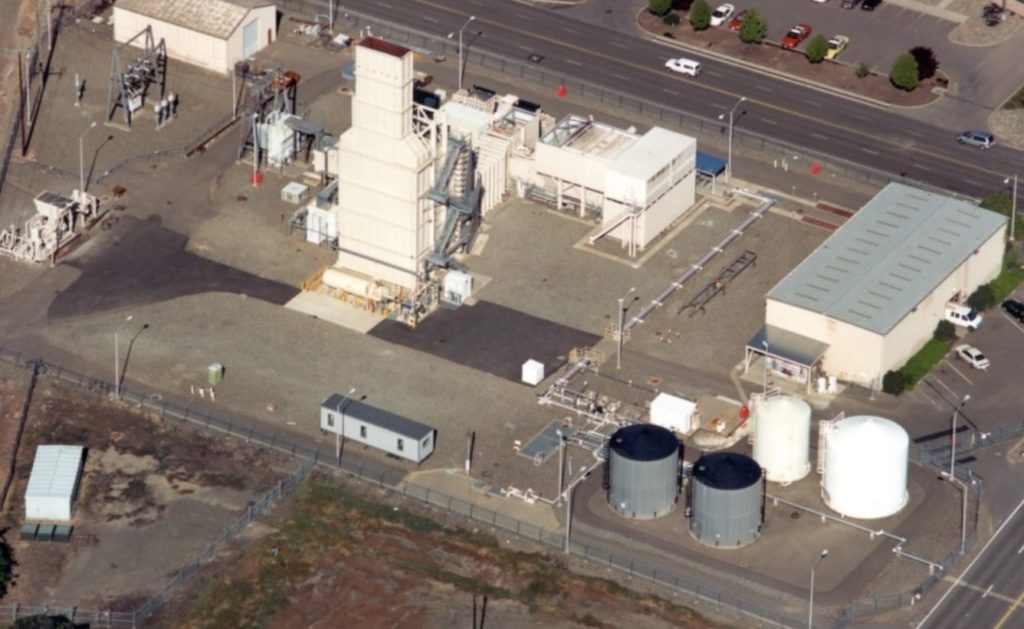
EETS worked with SMUD to provide engineering design services for the HMI and PLC-based controls upgrade, which was part of the GE Mark IV governor replacement for the 77MW unit at McClellan Air Force Base.
Sacramento, California
Proctor & Gamble Co-Generation
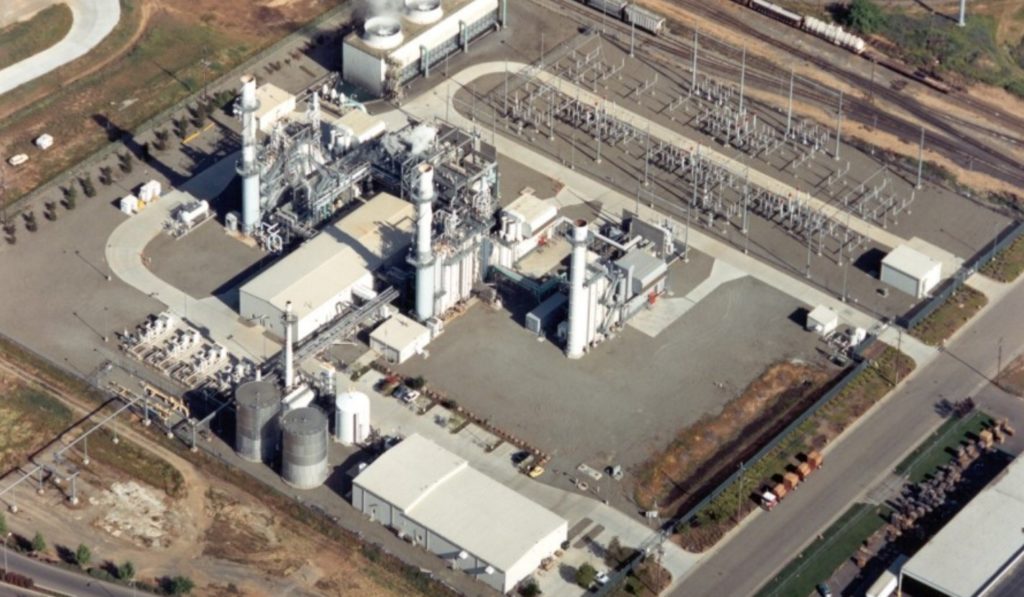
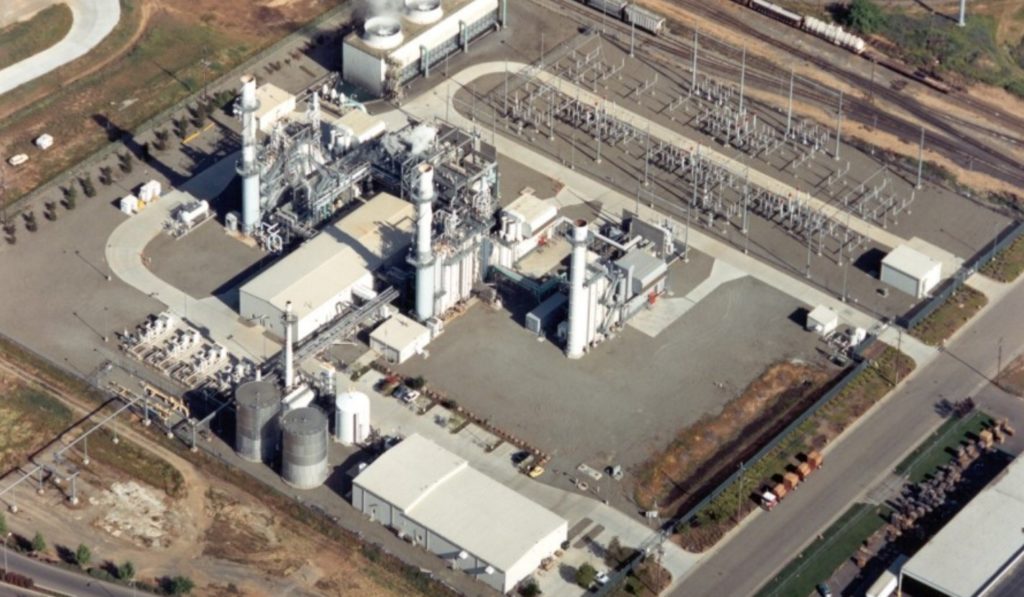
Sacramento, California
Campbell Soup Co-Generation
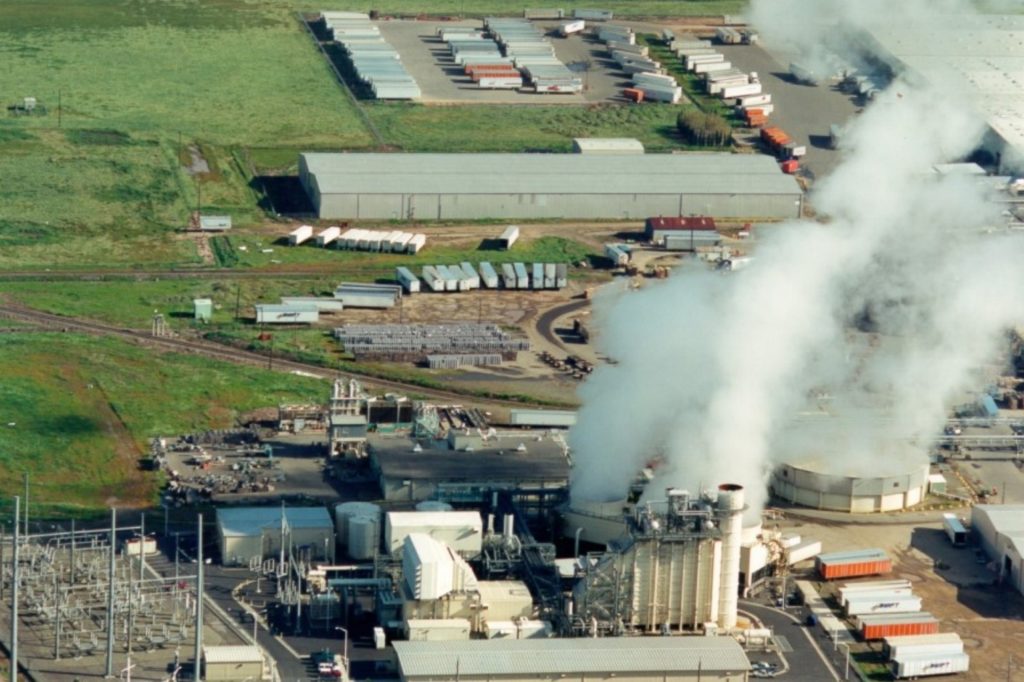
The Sacramento Municipal Utility District (SMUD) and Campbell Soup enlisted EETS to collaborate on a co-generation project. This facility, replacing large boilers, features a natural gas-fired combined cycle power plant. It supplies steam to the Campbell Soup facility and nearly 150MW of electricity to SMUD.
Furthermore, the facility emphasizes reducing pollutants and emissions, employing a selective catalytic reducer to monitor and control nitrous oxide emissions.
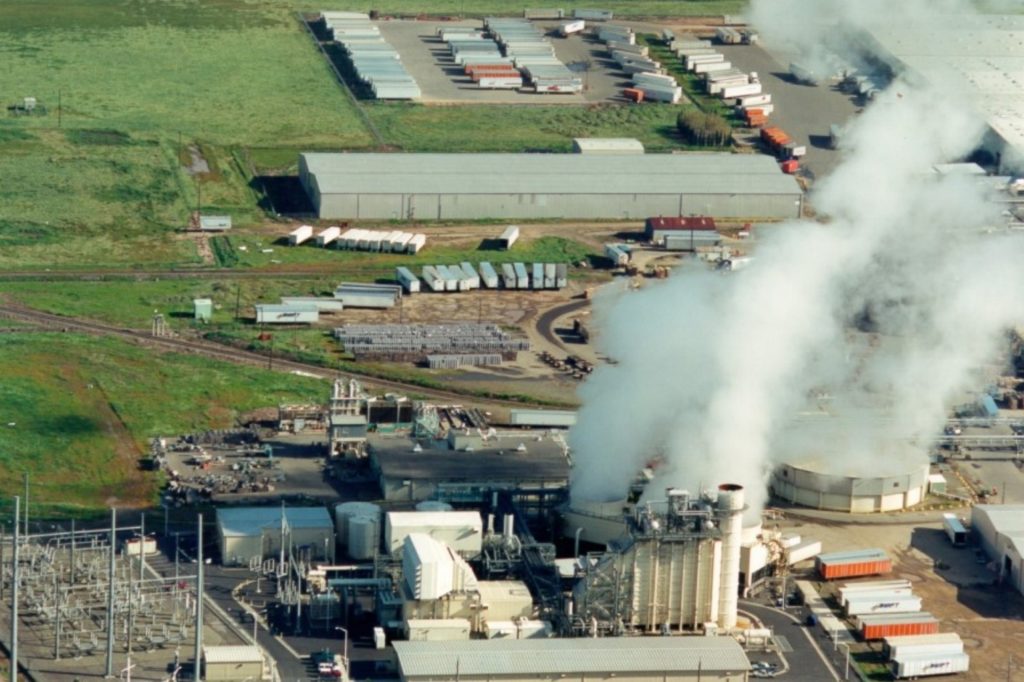
The Sacramento Municipal Utility District (SMUD) and Campbell Soup enlisted EETS to collaborate on a co-generation project. This facility, replacing large boilers, features a natural gas-fired combined cycle power plant. It supplies steam to the Campbell Soup facility and nearly 150MW of electricity to SMUD.