Combined Cycle
The term “combined cycle” describes a process where a gas turbine generator produces electricity, and the waste heat is then utilized to generate steam (and additional electricity) through a steam turbine. This method is highly efficient for large industrial plants, particularly in the food industry. Incorporating the steam cycle into the gas turbine cycle increases the electricity generated from a specific amount of natural gas. As a result, this leads to greater fuel efficiency and fewer emissions per unit of electricity generated than would be produced by the gas turbine alone.
SPOTLIGHT
Combined Cycle Projects
Sacramento, California
Proctor & Gamble
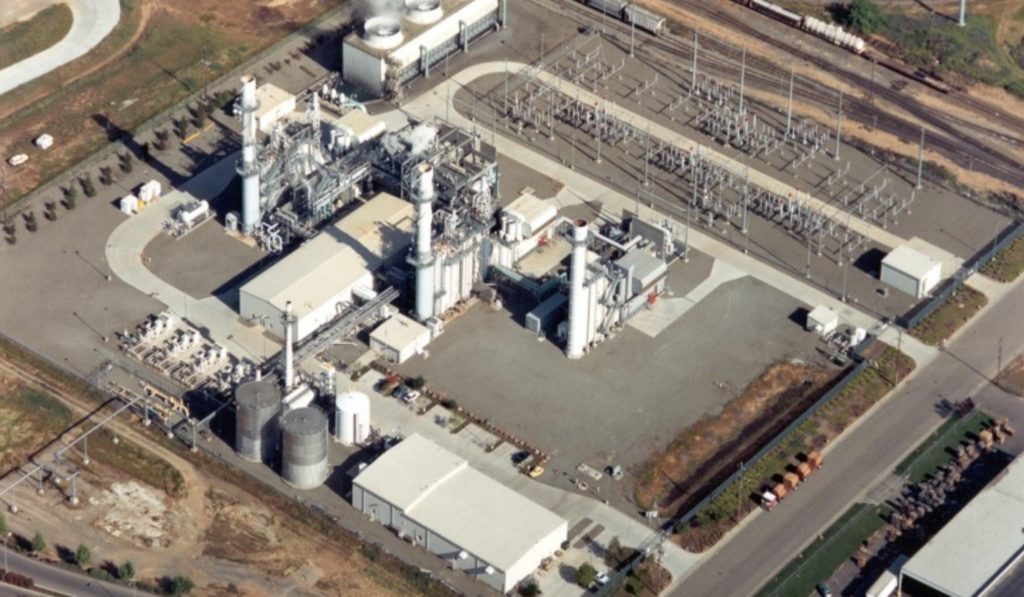
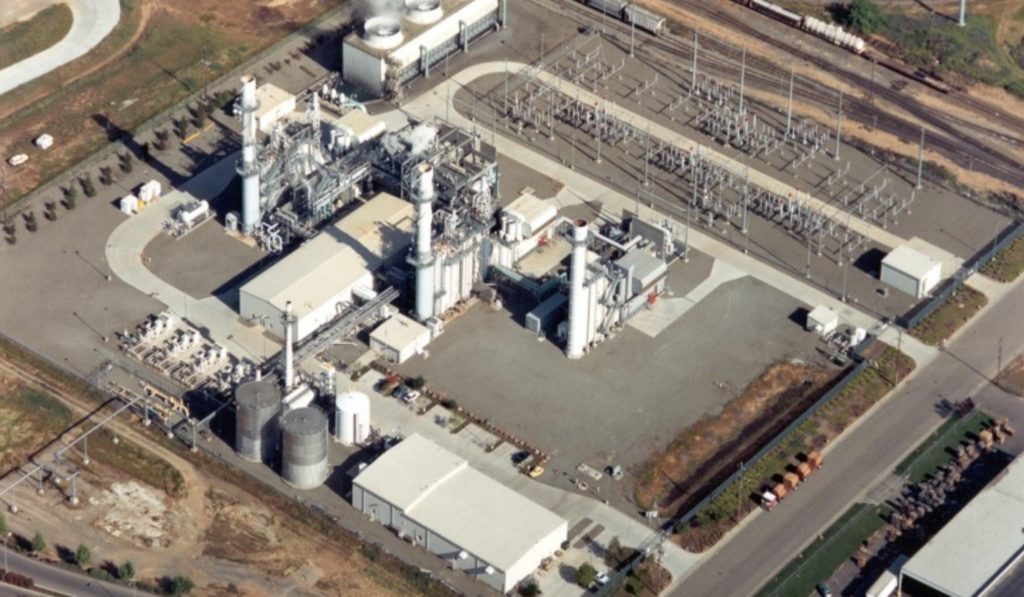
Sacramento, California
Campbell Soup
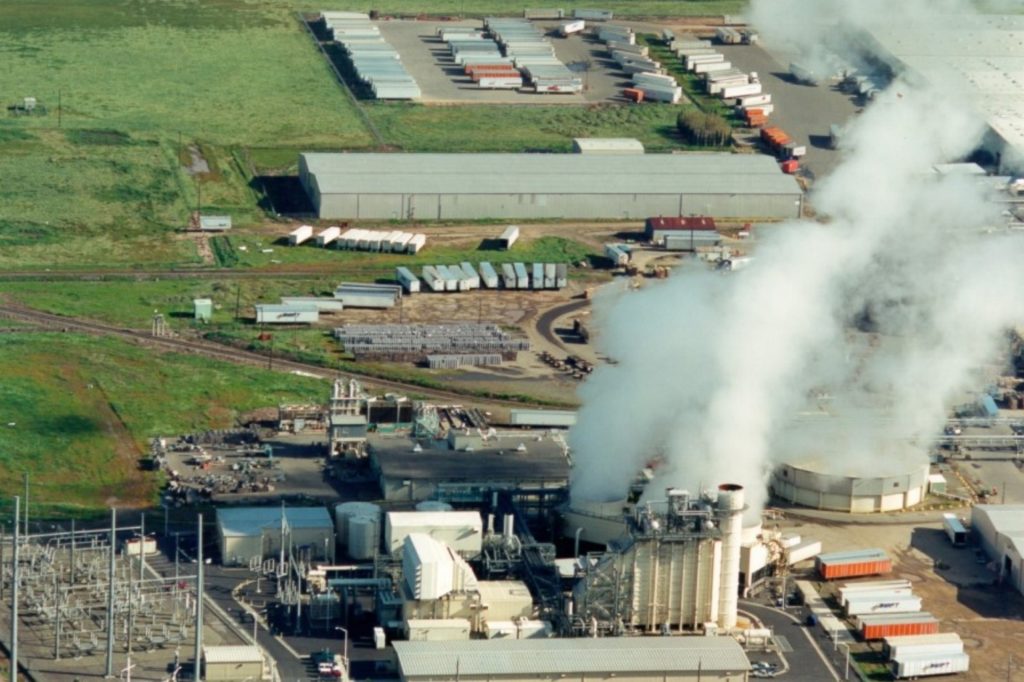
The Sacramento Municipal Utility District (SMUD) and Campbell Soup contracted EETS for the electrical infrastructure work on this co-generation project. The facility, designed to replace large boilers, employs Siemens gas turbines to generate 146MW of electricity. Furthermore, steam produced using recycled water from the soup plant is utilized in the soup processing operations.